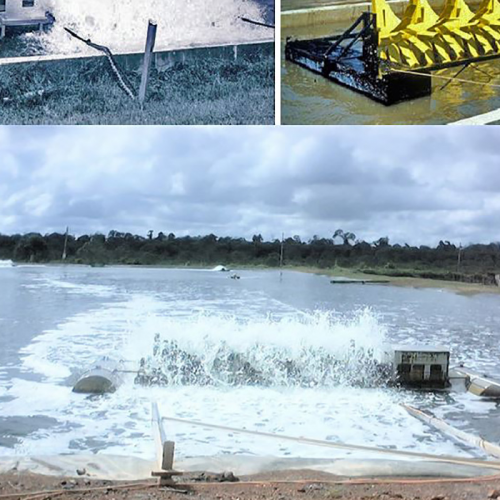
Energy Use in Aquaculture Pond Aeration
| Thu, 16 Jan 2020 - 10:36
Diesel and other internal combustion engines have much lower energy efficiencies than do electric motors (Table 1), but end-use energy from these two types of power units have different relationships with primary fuels. On average, the efficiency of grid electricity is about 33 percent from primary fuel to meter at the point of use. When 1 Megajoule (MJ, a unit of measurement of energy) of primary energy in coal or other fuel is combusted at a power generating plant, an average of about 0.33 MJ can be delivered to the 2-hp the motor of an electric aerator at a shrimp farm. Small motors are about 79 percent efficient, and 0.26 MJ of energy (0.33 MJ ×0.79) will be available from the aerator motor shaft – overall efficiency of 26 percent.
Boyd, aeration Pt. 2, Table 1
Electric motors |
Efficiency* (%) |
Small (<25 hp), stationary internal combustion engine |
Efficiency (%) |
1-4 hp |
78.8 |
Ethanol (E100) |
20-25 |
5-9 hp |
84.0 |
Liquid propane gas (LPG) |
25-30 |
10-19 hp |
85.5 |
Gasoline |
20-30 |
20-49 hp |
88.5 |
Diesel |
28-32 |
Table 1. Efficiencies of small, electric motors and small,
stationary internal combustion engines.
*https://www.engineering toolbox.com/electrical-motor-efficiency-d_655.html.
In truth, the overall efficiency at which fuel energy is converted to output shaft energy is similar for electric motors and internal combustion engines. Although internal combustion engines operating on different fuels have similar efficiencies, fuels have different energy contents per unit volume (Table 2). An engine running on ethanol will use a greater volume of fuel to produce the same energy output than will an engine operating on diesel fuel because ethanol has a lower energy content per liter than does diesel fuel. A fuel of lower energy content may be less economical or more economical than the fuel of greater energy content, depending on the price of each fuel per liter.
Boyd, aeration Pt. 2, Table 2
Fuel |
Energy content (1) |
Embodied energy factor |
Ethanol (E100) |
21.27 MJ/L |
1.49 (2) |
Ethanol (E85) |
22.58 MJ/L |
1.34 (3) |
LPG (liquid propane gas) |
23.48 MJ/L |
1.12 (4) |
Gasoline (no ethanol) |
31.80 MJ/L |
1.36 (4) |
Gasoline (10% ethanol) |
31.25 MJ/L |
1.37 (3) |
Biodiesel |
33.32 MJ/L |
1.69 (5) |
Diesel (No. 2) |
35.80 MJ/L |
1.28 (4) |
Electricity |
3.6 MJ/kW·hr |
2.50 |
Table 2. Energy content (lower heating value) of common
fuels and factors for including embodied energy in fuel energy calculations.
(1) https://afdc.energy.gov/fuels/fuel_comparison_chart_pdf.
(2)
http://large.stanford.edu/courses/2014/ph240/dikeou1/docs/ethanolnetenergy.pdf
(3) Calculated
(4) http://www.iea.org/statistics/resources/manuals/
(5) https://.adfc.energy.gov/files/pdfs/3229.pdf
Internal combustion engines, like electric motors, should be operated at around 75 percent full load to assure greater service life and efficiency. While engines consume fuel under no load, the percentage full-load fuel used when an engine is idling at no load is lower than the percentage of full-load electricity used by a motor running under no load (Fig. 1). The fuel consumption of an engine declines with load in an approximately linear manner, and load can be estimated from fuel use. A typical, small diesel engine uses about 0.23 L/hr. fuel per horsepower·hour (0.31 L/hr. per kilowatt·hour).
Fig. 1: Load versus fuel use by internal combustion engines and current use by electric motors (prepared with information from http://dieselserviceandsupply.com/Diesel_Fuel_Consumption.aspx and from http://energy.gov/sites/prod/files/2014/04/f15/10097517.pdf).
Output shaft speeds of small, internal combustion engines usually are around 3,000 rpm. The most common aerator in shrimp farming is the paddlewheel aerator, and paddlewheels usually are operated at speeds of 60 to 120 rpm. Output shaft speeds of both electric motors and internal combustion engines must be reduced for paddlewheel applications.
Drive trains
Propeller-aspirator-pump aerators and vertical-pump aerators operate at the speed of their motor shafts. Only a single coupling usually is necessary between motor and aerator shaft. However, these aerator types are not as common in shrimp farming as the paddlewheel aerator.
There are three main types of paddlewheel aerators. The 1- and 2-hp Asian floating, electric paddlewheel aerators, have a motor with a two directional gear-reducer mechanism mounted on floats, with a shaft upon which the paddlewheels are mounted extending from each side of the gear-reducer.
Views of Asia-style, small, electric, floating paddlewheel aerators.
The second type, a 5- or 10-hp aerator, which will be called a U.S. catfish pond paddlewheel aerator is used sometimes in shrimp ponds in the western hemisphere. The motor of this kind of aerator is mounted on one end of a flotation platform, there is a gearbox or other speed reduction mechanism between the motor, and a hub upon which paddles are welded to form a paddlewheel.
Views of U.S. catfish pond paddlewheel aerators.
In the first two kinds of aerators, the rotating shafts of the paddlewheels must be supported by bearings or other mechanisms that allow rotation with a minimum friction loss. These aerators have relatively high efficiency of energy transfer from the motor shaft to paddlewheel shaft – the efficiency usually is 90 to 95 percent.
The third type of paddlewheel aerator is the so-called long-arm aerators popular in Thailand and some other Asian countries. The paddlewheel is mounted on floats installed in the pond, and the engine or motor is mounted on the pond bank. The speed of the engine or motor output shaft usually is reduced by V-belts or chains and sprockets in which two shafts (often called jackshafts) are used to diminish the motor output shaft speed to the desired paddlewheel speed.
The equation for relating speeds of driver shafts to driven shafts for pulleys (sheaves) and belts are:
D1 × RPM1 = D2 × RPM2
where D1 and D2 = pitch or flat-face diameters of driver and driven pulleys, respectively, and RPM1 and RPM2 are speeds of the driver and driven shafts, respectively.
The equation for speed reduction by chains and sprockets is similar to that for speed reduction by belts and pulleys:
T1 / T2 = RPM1 / RPM2
where T1 and T2 = teeth on the driver and driven sprockets, respectively, and RPM1 and RPM2 are sped off the driver and driven shafts, respectively.
The principle of the jackshaft mechanism often used to reduce motor speed when driving a paddlewheel aerator from an engine or motor on the pond embankment can be explained by an example. A 12-cm pulley could be placed on the motor shaft (1,735 rpm) and a 70-cm pulley mounted on a short-driven shaft mounted in a metal frame. The driven shaft would turn at 297 rpm [(12 cm)(1735 rpm) = (70)(RPM2); RPM2 = 297] which is still too fast for the paddlewheel.
The first driven shaft could have a 15-cm pulley attached to it and connected by a belt with a 50-cm pulley to a second shaft mounted in the metal frame. The second driven shaft would rotate at 89 rpm [(15 cm)(297 rpm) = (50 cm)(RPM2); RPM2 = 89] – a speed suitable for the paddlewheel. The two jackshafts would have to be firmly mounted in bearings supported in a metal frame beside the motor shaft.
The output shaft of the jackshaft mechanism must be connected by a driveshaft to the aerator shaft. The drive shaft must extend downward at an angle to the shaft of the paddlewheel aerator mounted on floats on the pond. This usually is accomplished by connecting shafts with the aid of universal joints. At many farms, directional gear mechanisms also are used in the drive train to allow power to be distributed to multiple floating paddlewheels.
The devices used to slow rotation speeds, connect shafts, and change directions of power transmission in the drive train incur energy losses. Typical efficiencies are V-belt drives, 90 to 95 percent; roller chain drives, 95 to 98 percent; gearboxes, 85 to 90 percent. Energy loss is small (~1 to 2 percent) in couplings that are properly designed and installed, but misalignment of couplings and vibrations in shafts results in much larger losses of energy.
At Asian shrimp farms, the shafts between the driver shaft of the jackshaft mechanism and the aerator shaft usually is a long, 3.75 to 5 cm diameter galvanized water pipe which vibrates considerably and misalignment between shafts and couplings are obvious. There are no studies (to my knowledge) of energy loss in the drive trains of long-arm paddlewheel aerators. The overall loss is likely at least 30 to 40 percent when only one aeration unit is operated from a motor or engine of a long-arm aerator. Greater losses no doubt are incurred with multiple long-arm aerators powered from a single-engine or motor.
Potential for energy conservation
The large, floating electric paddlewheel aerators used on U.S. catfish farms are about 30 percent more efficient in transferring dissolved oxygen than are floating, electric aerators used in Asia. Based on the “rule of thumb” of 2.5 hp/MT shrimp for Asian paddlewheel aerators, the aerator rate could be reduced to 1.75 hp/MT of shrimp by use of the U.S.-style paddlewheel aerators. The drive train efficiencies are probably about 70 percent for long-arm aerators and 90 percent for Asian, floating, electric paddlewheel aerators. As a result, about 3.22 hp/MT of shrimp should be required for long-arm paddlewheel aerators. Energy use would be 11.5 GJ/MT of shrimp with Asian floating, electric aerators.
By using long-arm aerators, the energy use would be increased by the ratio of 3.22 hp/MT/2.5 hp/MT, which would result in the energy use of 14.8 GJ/MT. Likewise, by use of the larger US floating paddlewheel aerators, energy use could be reduced to 8.1 GJ/MT. According to an average aeration schedule of 16 hr./day and 80 days/crop, aerators would run for 1,440 hours/crop or 4,637 hp·hr for a diesel-powered, long-arm aerator. At fuel consumption of 0.23 L/hp·hr, 1,067 liters of diesel fuel would be consumed per MT of shrimp. This amounts to 38.2 GJ/MT of shrimp produced.
Perspectives
The estimates above are for direct energy use. Applying embodied energy factors for fuels from Table 2 give total energy use as the U.S. style, floating, electric paddlewheel aeration, 20.25 GJ/MT shrimp; Asian style, floating, electric paddlewheel aerator, 28.8 GJ/MT shrimp; electric-powered, long-arm aerator, 37 GJ/MT shrimp; and diesel-powered, long-arm aerator, 48.9 GJ/MT shrimp.
These calculations are based on certain assumptions and obviously subject to uncertainty, but they suggest that the efficiency of shrimp pond aeration could be improved to save a considerable quantity of energy. Assuming that 4 million MT of shrimp are produced in aerated ponds, each 1 GJ/MT reduction in energy use would reduce energy use in penaeid shrimp farming by 4 million GJ or roughly 830 million kW·hr (71,367 MT of oil or 488,234 barrels of oil equivalent).
There would be both energy conservation and farm-level economic benefits to improving the energy efficiency of shrimp pond aeration.
Source: Global Aquaculture Alliance