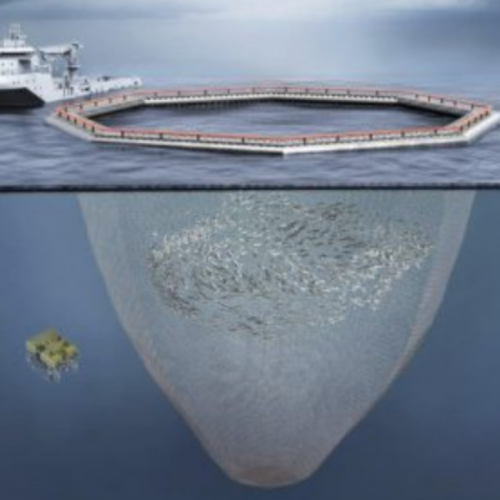
Top Copper Maker Wieland Sees End to Escapes, Will Improve Fish Health With Brass Mesh Cages
| Mon, 13 Apr 2020 - 10:48
Sea cage makers and copper producers are on the verge of delivering an important disruption to the global aquaculture industry.
Copper, which prevents biofouling because of its antimicrobial properties, can be used in aquaculture cage netting and makes sea pens stronger and capable of withstanding hurricanes and typhoons. Copper alloy mesh could make aquaculture feasible in areas of the world that suffer big storms, such as the South China Sea and the Mediterranean.
German copper materials maker Wieland has slowly bided its time with an aquaculture investment, patenting cage mesh technology in 2015, and acquiring a handful of customers in Australia, China, and Hawaii. The company is in the process of convincing Norway’s salmon farmers to use the technology, said Daniel Steitz, Weiland's head of innovation at BU EX bei Weiland Group.
“The aquaculture industry is now facing a situation where it is going more and more offshore, and we see more and more benefits for our material,” Steitz told Undercurrent News.
Wieland’s incursion into sea cages is part of a broader trend of innovators from other industries targeting the high-growth aquaculture industry, bringing solutions to key pain points. The Ulm, Germany-based company is the world’s largest maker of copper alloys, producing over 180 materials for thousands of products.
Brass is the alloy of copper and zinc and has been used since Ancient Greece. Copper, besides being tougher than nylon or polyester nets, is antimicrobial and prevents biofouling. This prevents the accumulation of microorganisms, plants, algae, barnacles and mollusks, that tend to accumulate on traditional nylon netting and limit the flow on water into a cage.
Biofouling on nets was deemed as the cause of the Cooke net pen collapse in the Puget Sound in 2017, where 200,000 Atlantic salmon escaped, allegedly affecting wild salmon river runs. Cooke reportedly hadn’t had time to carry out maintenance on the nets since it bought the assets from troubled Icicle Seafoods the year before.
Wieland is not alone in looking to apply antimicrobial copper in aquaculture. The International Copper Institute in South Korea has been researching copper cages for several years to develop an aquaculture industry around the Korean peninsula, said country manager Chris Lee. Prototype cages have been tested by STP Donghae, an offshore salmon farmer in South Korea. The Asian country has ambitions to farm bluefin tuna and the technology will help them in that quest, Lee said.
Copper mesh is a much more expensive component than traditional plastic but comes into its own in new submersible pen designs, as it solves the problem of needing to frequently clean nets. Donghae needs to submerge cages for several weeks during the Korean summer when surface temperatures can approach 30 degrees Celsius (86 degrees Fahrenheit).
Norway does not yet use submersible cages but is a great fit for Wieland’s business because local laws require salmon farmers to clean nets every 5 to 10 days, Steitz said. This raises an animal welfare issue because they can get gill irritation during every cleaning process, he said. Wieland is going to do some testing of its product in the Norwegian market in 2020.
Increasingly bad weather is putting pressure on aquaculture farmers to use stronger cages. Spain's aquaculture farmers lost half of their entire annual output earlier this year in Storm Gloria and Bakkafrost announced March 8 that it lost millions of fish in a storm on the Faroe Islands.
Copper alloy netting cannot be fitted on several conventional cage designs and it disrupts stability, Steitz said. The industry will only likely to adopt this technology as they move further offshore and have further need to reduce maintenance work and require more robust specifications, he said.
Competition in brass and copper
Wieland will face competition. Italy’s Badinotti, a global netting leader and cage-maker installed copper-alloy mesh on its Oceanis range of cages for an offshore farm in Mexico.
“Copper nets are mostly used for parasites and it’s also common when you have very heavy problems with the fouling of the net due to the high temperature of the water,” Caprile told Undercurrent.
Copper netting in warmer waters also eliminates the need for double netting used to stop predators. Badinotti has also come up with a hybrid solution, using the filaments of copper to create a net that is lighter and has textile flexibility.
GiliOcean, an Israeli cage maker, sees the combination of submersible cages and copper netting as the two main factors in making cages escape-proof. The company has tested its offshore cages in waves as high as 11 meters, using a pioneering design that will be tested by Ocean Era in the Gulf of Mexico.
InnovaSea Systems, part of the Cuna del Mar family of companies owned by the billionaire Walton family, will use brass mesh on future iterations of its submersible SeaStation pen. The SeaStation is used by Open Blue Cobia in offshore Panama, which is located 10 miles out to sea.
Brass netting “essentially eliminates the risk of having farmed fish or predators end up on the wrong side of the net,” Langley Gace, a senior vice president at InnovaSea, told Undercurrent. “It also keeps the surface of the pen clean, allowing more oxygen rich water to flow through to the fish to improve their overall health.”
Serving exacting customers
One area where Wieland can compete strongly is in its track record of serving demanding customers, Steitz said. The German company supplies the automotive industry with copper alloy products, and these have to be made to exacting standards to avoid corrosion. The sea is one of the most corrosive environments there is, he said.
“A material that is 100% in seawater conditions needs to be very good, needs to have very good corrosion resistance, a certain hardness and temperament to withstand all the permanent movement,” he said. “You cannot make this without having deep material knowledge and we have more than 100 people in our research department, only doing material research.”
Source: Undercurrent News