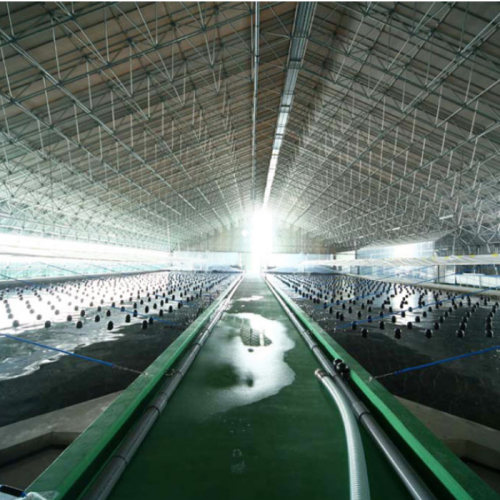
Power Move: Japanese Energy Firm Getting in on RAS Shrimp
| Tue, 23 Feb 2021 - 12:05
Japan, a nation with a traditionally high seafood consumption rates, sees land-based aquaculture as a way to secure supplies of popular fish species – including shrimp – in an environmentally friendly manner. Now, some unexpected Japanese firms are entering recirculating aquaculture systems (RAS) production, continuing a countrywide trend.
Last October, Kansai Electric Power (KEPCO) announced plans to build an RAS facility, starting in January 2021, in Iwata City, Shizuoka Prefecture, near Tokyo.
KEPCO aims to farm Pacific whiteleg shrimp starting in March 2022 under the name Kaiko Yukinoya Co. Ltd. The new company will use a system called the Indoor Shrimp Production System (ISPS), jointly developed by aquaculture engineering firm International Mariculture Technology Engineering Inc. (IMTE) and the Japan International Research Center for Agricultural Sciences (JIRCAS).
ISPS consists of an automatic wave-generating apparatus and a vertical pump that conserves energy. A robotic cleaner automatically removes solid debris from the bottom of the tanks while an oxygen-generating system can be adjusted according to biomass. The system also uses low-salinity, high-hardness water and offers a quasi-natural environment with artificial seaweed that prevents cannibalism by giving newly molted shrimp a place to hide.
According to Setsuo Nohara, executive advisor at IMTE, Japan’s annual shrimp production derives almost entirely from the Kuruma prawn (Marsupenaeus japonicus) and is only 1,500 tons a year (IMTE makes a small contribution to the domestic market with whiteleg shrimp Litopeneaus vannamei produced at its plant in Myoko City, Niigata Prefecture – see photos).
“We are planning on production levels of 80 tons a year, which amounts to 5 percent of Japan’s current total aquaculture production of shrimp,” Nohara told the Advocate. “However, Japan currently consumes nearly 250,000 tons of shrimp per year, and this supply depends almost entirely on imports of frozen shrimp from overseas. In this way, it may be calculated that Japan’s self-sufficiency in shrimp is only 5 percent at present. Therefore, we expect the new plant to make a significant contribution to Japan’s markets.”
Harvesting shrimp at the IMTE whiteleg shrimp plant in Myoko City, Niigata Prefecture.
“We’re delighted that KEPCO, one of Japan’s foremost companies, has adopted our technology for their first entry into the food production business,” he continued. “We’re confident that Kaiko Yukinoya will be an example of a vibrant shrimp culture industry in Japan that is sustainable from a business standpoint and compatible with today’s needs to ensure environmentally friendly aquaculture production. The new plant will help us achieve an economy of scale in production and we hope that we can also offer it outside Japan to do our share in assisting in the industry.”
IMTE and JIRCAS have been developing technology for the agriculture, forestry and fisheries sectors for 20 years. IMTE has been producing shrimp commercially for more than 12 years, while JIRCAS is a national institute aiming to provide a stable supply of agricultural, forestry and fishery products and resources through research and technology development. Together, they’ve been introducing RAS shrimp culture based on the ISPS concept to countries such as Vietnam and India through consulting opportunities.
Kaiko Yukinoya Co. Ltd arrives in Japan amidst an increasing move in the country toward RAS. The trend is driven by the technology’s promise to limit negative environmental impacts and tighten biosecurity. But questions remain as to whether RAS can be profitable, given the high amount of equipment and water treatment facilities that are required.
“Initial investment costs are very high, but Iwata City has helped us to clear this problem by offering generous measures to build a shrimp plant in their city as Kaiko Yukinoya is established,” said Nohara and Dr. Marcy Wilder, senior research scientist at JIRCAS. “Meanwhile, building a very large-scale shrimp plant will sufficiently lower unit costs for such things as labor, electricity and feed, thus realizing a true economy of scale. The system also has virtually no environmental impact. In fact, at the conclusion of a production cycle, since the water we use is very low salinity and sufficiently clean according to Japanese sewerage standards, it can be disposed of easily and according to standard methods.”
The economic benefits of land-based farming in Japan are also worth noting, according to Dr. Junpei Shinji of the University of Tokyo. He is a co-author of a bio-economic analysis into Japan’s closed shrimp farming that was recently featured in the Advocate.
“Such benefits depend on the ability to improve and artificially control rearing conditions,” he said. “But unforeseen problems may occur. In our analysis, we predicted that there may be unidentified but critical factors that increase mortality, possibly induced by the cumulative death of individuals in the closed system. One key point that’s necessary for efficient economic management is managing shrimp populations within the system. The timing of harvests may also be an easy solution to implement.”
Nohara and Wilder have high hopes that their ISPS technology could set the stage for more RAS-related enterprises in Japan. At the same time, both have found that many Japanese consumers have a high awareness of what constitutes seafood quality and are keen to learn what species of shrimp or fish they are eating, where it comes from and how it’s produced. Prominent features in Japanese media have made IMTE and JIRCAS’s work more transparent, with consumers interested to learn that shrimp can be produced in an area like Myoko – a cold, mountainous region that’s far away from the ocean.
IMTE-produced Myoko Snow Shrimp, vacuum-packed for Japanese retail outlets.
Does this mean more land-based farming in Japan?
“We believe there is huge potential for RAS to take off in this country,” said Wilder. “But it must be sustainable. Not only must the technology work but it must also be economically viable. If the proprietor of an enterprise using RAS technology goes out of business, that technology is not sustainable. We also think of the word sustainable in the usual way – being good for the environment and society. For sustainable shrimp production, both conditions must be met.”
High demand for seafood throughout Japan presents a favorable outlook for companies like KEPCO seeking to enter the aquaculture sector, Wilder said.
“While a certain amount of conventional aquaculture takes place, land available for use in RAS systems is subject to certain limitations from both legal and suitability perspectives,” she said. “Nevertheless, there is great potential to convert unused farmland into sites for RAS enterprises, and many people have considered utilizing abandoned public facilities such as school buildings in sparsely populated areas. In this way, the relevant sections of the Japanese government are giving consideration to measures to further promote RAS in this country. We think that the time is right for land-based aquaculture production here.”
Source: Global Aquaculture Alliance